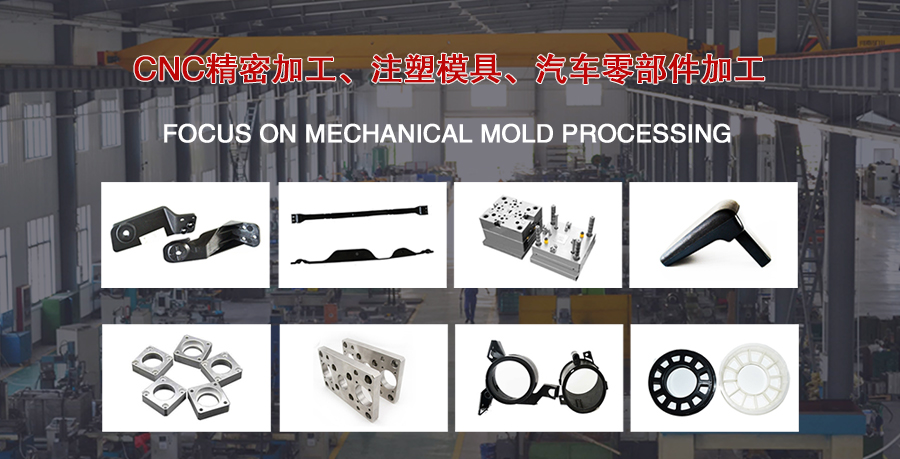
在现代制造业中,注塑模具扮演着至关重要的角色。注塑模具的质量直接影响到最终产品的性能、外观以及生产效率。因此,如何提升注塑模具的质量,成为了行业内各大企业关注的焦点。本文将从多个角度分析提升注塑模具质量的关键因素,帮助企业在技术竞争中脱颖而出。
一、模具设计是质量提升的基础
模具的设计阶段是注塑模具质量提升的首要环节。设计不合理的模具往往导致产品质量不稳定,甚至影响到生产的顺利进行。为了确保注塑模具的质量,设计人员需要遵循以下几个原则:
合理的结构设计:在模具的结构设计上,必须考虑到注塑成型过程中可能出现的各种问题,如收缩、变形、翘曲等。优化的结构设计不仅可以提高模具的使用寿命,还能够减少生产中的瑕疵,提高产品的一致性。
合适的冷却系统设计:模具的冷却系统设计对于保证产品的成型质量至关重要。冷却不足会导致模具温度不均,进而影响产品的尺寸精度和外观。合理布置冷却通道,可以加速模具的冷却速度,避免因温差过大引发的成型缺陷。
精密的模具配合:模具的各个部件需要高精度配合,尤其是模具的型腔和型芯。这要求设计师在设计时就要考虑到各个部件的公差要求,确保配合的精密性。高精度的配合不仅可以提高成型产品的精度,还能延长模具的使用寿命。
合理的排气设计:排气不良会导致产品成型不完全,甚至出现气泡、烧焦等缺陷。因此,在模具设计中,排气设计非常重要。优化的排气设计可以确保气体顺利排出,保证注塑过程的顺畅。
二、优质材料的选择对模具质量至关重要
模具材料的选择直接影响模具的硬度、强度、耐磨性及耐腐蚀性。不同的注塑产品需要选择不同的模具材料,以下是几个常见的模具材料及其特点:
钢材:钢材是最常用的注塑模具材料之一。高品质的钢材不仅能够提高模具的硬度和强度,还能够有效延长模具的使用寿命。常见的钢材包括P20、H13、S136等,这些钢材在加工过程中表现出较好的稳定性和耐磨性,适合生产要求较高的注塑模具。
铝合金:铝合金模具因其较轻的质量和较好的导热性能,适用于低批量生产和小型产品的注塑加工。铝合金模具的冷却速度较快,有助于提高生产效率,但其耐用性相对较低。
硬质合金:硬质合金材料具有极高的硬度和耐磨性,适合于高精度、高强度要求的注塑模具。硬质合金模具的使用寿命非常长,尤其适用于高温、高压条件下的注塑成型。
在选择材料时,企业应根据实际需求权衡各种因素,如成本、生产周期、模具使用寿命等,确保所选材料符合模具的使用要求。
三、的加工工艺是提升质量的保证
注塑模具的加工工艺直接决定了模具的精度和质量。技术的不断发展,越来越多的加工工艺被应用到注塑模具的生产中,这些工艺有效提升了模具的质量和生产效率。
精密加工技术:精密加工技术在模具的加工过程中起着至关重要的作用。通过高精度的数控加工设备,可以精确控制模具的尺寸公差,确保模具的精度达到设计要求。精密加工技术不仅能够提升模具的质量,还能提高模具的生产效率,减少废品率。
电火花加工(EDM):电火花加工技术广泛应用于模具制造中的细微加工。它可以高效加工复杂的模具细节,尤其是在硬质合金等高硬度材料的加工中表现尤为突出。电火花加工不仅能够保证模具的精度,还能够避免传统机械加工中的刀具损耗。
激光加工技术:激光加工技术在模具制造中应用逐渐增多。激光加工具有精确度高、加工速度快等优点,适用于复杂型腔的加工。激光加工不仅提高了模具加工的精度和效率,也为模具设计师提供了更多的设计自由度。
表面处理技术:模具的表面处理技术对于提高模具的耐用性和稳定性至关重要。常见的表面处理技术包括镀铬、氮化处理等,这些技术能够有效提高模具表面的耐磨性、抗腐蚀性以及耐高温性能。
四、质量控制和检测不可忽视
质量控制和检测是注塑模具生产过程中不可忽视的环节。通过严格的质量控制和检测手段,能够及时发现和解决生产中存在的问题,确保模具的质量达到预期要求。
模具试模:模具试模是验证模具设计和制造是否符合要求的重要环节。通过试模可以发现模具在实际生产过程中可能出现的各种问题,如成型不良、翘曲变形等。根据试模结果调整模具设计或加工工艺,确保最终产品的质量。
检测技术:采用现代化的检测技术,如三坐标测量机(CMM)、激光扫描等,可以精确测量模具的各项尺寸和公差,确保模具符合设计要求。使用这些检测设备还可以高效地进行大批量的模具检验,确保模具的高质量。
耐用性测试:在模具制造完成后,进行耐用性测试也是非常重要的。这些测试可以帮助判断模具在长时间使用后是否仍然保持高性能,是否存在材料疲劳或其他潜在问题。