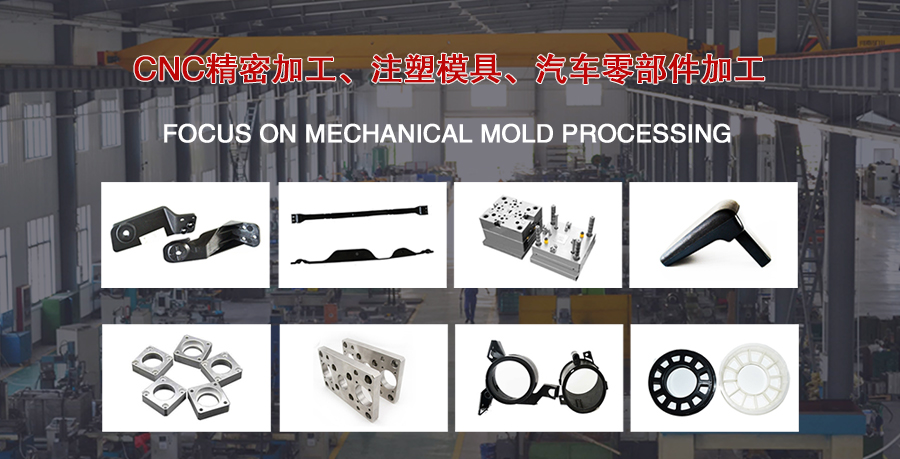
注塑模具作为注塑成型过程中至关重要的工具,其设计质量直接影响到产品的生产效率和产品的质量。在注塑模具设计过程中,许多设计师和工程师往往会忽视一些细节问题,导致模具的设计不完善,甚至影响生产流程的顺利进行。本文将总结并解析注塑模具设计中的常见误区,并提供应对这些问题的策略,帮助设计师规避常见的设计错误,提升整体设计水平。
1.忽视材料特性与模具设计的匹配性
在注塑模具的设计过程中,很多设计师往往忽视了材料特性对模具设计的影响。不同的塑料材料具有不同的流动性、收缩性、硬度以及热膨胀特性,设计师若没有深入了解这些特性,很容易在模具设计上出现问题。例如,某些高粘度塑料材料可能会在注射时导致填充不均或材料滞留,进而影响成型质量。
解决方案:设计师需要充分了解所用材料的特性,并将其融入模具设计过程中。例如,在设计冷却系统时,针对不同塑料材料的热传导性能设计合理的冷却通道;在设计注射系统时,根据材料的流动性来调整喷嘴、流道和浇口的位置与尺寸,避免产生气泡、短射等质量问题。
2.模具结构设计不合理
模具的结构设计直接关系到注塑产品的质量与生产效率。如果模具的结构不合理,可能导致产品的尺寸精度无法保证,甚至引发模具损坏。常见的错误包括浇口位置选择不当、模具的锁模力分布不均以及冷却通道设计不合理。
解决方案:模具的结构设计应遵循一定的原则,确保各部分的配合精确、功能合理。设计时,应根据注塑件的形状、大小、壁厚等特性,选择合适的浇口类型与位置,避免局部应力集中和材料流动不均。合理设计模具的锁模力,使其均匀分布,可以有效避免模具变形与损坏。在冷却系统设计上,要确保冷却通道均匀分布并能充分冷却模具表面,减少成型周期并提高生产效率。
3.忽视模具排气设计
在注塑过程中,排气不畅会导致气体滞留,影响模具的填充过程,甚至可能造成模具损坏或产品质量问题。很多设计师忽视了模具排气系统的设计,导致气体无法及时排出,进而影响注塑成型的精度与质量。
解决方案:设计排气系统时,应根据模具的形状和材料的流动性合理安排排气孔的位置和大小。排气孔通常应设置在模具的最远端,以便将气体尽早排出,防止气泡、烧焦等现象的出现。避免排气孔的过度堵塞,确保气体流通畅通,提升产品的成型质量。
4.过度依赖仿真软件,忽视实际生产经验
注塑技术的发展,越来越多的仿真软件被用于模具设计和优化。仿真软件可以帮助设计师预测注塑过程中可能出现的问题,很多设计师过度依赖仿真软件,忽略了实际生产中的经验和实际数据。这种依赖可能导致仿真结果与实际情况不符,从而无法真正解决生产中的问题。
解决方案:尽管仿真软件是设计中非常重要的工具,但设计师应将仿真结果与实际生产经验结合起来,综合考虑生产中可能出现的变化因素。例如,在仿真过程中,可以通过实际生产数据进行校正,调整设计方案,确保设计的可行性与实际效果。
5.缺乏对模具维护与使用寿命的考虑
模具作为一种高精度工具,其使用寿命与维护保养密切相关。在设计阶段,如果没有考虑到模具的维护与更换容易性,可能会在使用过程中导致模具损坏或无法继续使用,增加了生产成本与停机时间。
解决方案:在模具设计阶段,设计师应考虑到模具的维护与维修便捷性。例如,可以设计易于拆卸和更换的部件,便于在使用过程中进行检查与修复。设计师还应根据实际生产的需求,对模具的耐用性进行优化,选择合适的材料与表面处理工艺,延长模具的使用寿命。
6.忽视模具设计的可加工性
在模具设计时,有时设计师可能会因为追求过高的精度或过于复杂的结构而忽视模具的加工性。这不仅会增加制造成本,还可能导致生产周期延长,甚至无法按时完成生产任务。
解决方案:设计时应考虑模具的加工难度与可行性,选择合适的设计方案来降低生产难度和成本。合理利用标准化部件和模具系统,避免过多复杂的加工工艺。设计师需要与模具制造厂密切合作,确保设计方案能够在规定的生产条件下顺利实施。
注塑模具设计不仅仅是关于结构的创造,更多的是在不同因素间找到平衡,从材料、工艺到生产成本和维护等方面进行综合优化。为了实现最佳设计,设计师需要注重细节,并时刻关注新技术的发展,力求在注塑过程中减少错误,确保高效且精准的生产过程。
7.模具设计与生产工艺脱节
模具设计与生产工艺之间的紧密联系是许多设计师常常忽视的一大问题。模具的设计应当与实际的生产工艺相匹配,如果忽略了生产工艺的约束条件,可能会导致生产过程中出现各种问题。
解决方案:模具设计时,必须充分考虑到实际生产工艺的限制,包括注塑机的性能、成型时间、原料的特性等。设计师应当与生产部门紧密合作,了解生产线的实际需求和设备条件,从而设计出最适合的模具,避免出现模具无法适配现有设备的情况。
8.过早定义设计的细节
在注塑模具设计的初期阶段,许多设计师会过早地对模具的细节进行定义,如形状、大小和细部特征等。虽然这可以提高设计效率,但若后期发现设计存在问题时,调整和修改会非常复杂且昂贵。
解决方案:注塑模具设计应采取逐步优化的方式。初期阶段,重点确定模具的基本框架和功能性设计,避免过早进入细节。待基础设计稳定后,再对细节部分进行不断优化,以便根据实际情况作出调整,避免过多的返工。
9.忽视模具设计的可调性
模具设计过程中,如果没有考虑到模具的可调性,可能会在生产过程中因为需求变化而导致模具无法适应不同的生产条件。模具的可调性包括尺寸调整、温控系统调整等方面。
解决方案:在模具设计时,应该尽量设计一些可调部件,方便在生产过程中根据不同需求进行调整。例如,注塑机的温控系统可以设计成可调的,从而应对不同材料的加工需求;模具的尺寸调整则可以通过设计可更换的模芯或调节板来实现。
10.忽略环境与安全要求
模具的设计不仅需要考虑生产的效率与质量,还需要兼顾环境保护与安全要求。注塑过程中,可能会产生有害气体或废料,如果没有设计合适的排放和处理系统,不仅可能造成环境污染,还会对工人的安全构成威胁。
解决方案:设计时应严格遵守环保法规和安全标准,设计合适的通风和废气处理系统。模具的设计要尽量减少生产过程中的浪费和有害物质的产生,保护环境并保障工人安全。
总结而言,注塑模具设计是一个复杂且细致的过程,任何一个小小的失误都可能导致严重的生产问题。设计师只有在充分考虑材料特性、模具结构、生产工艺等多方面因素后,才能设计出高效、稳定、符合生产需求的模具。在实际工作中,设计师需要不断积累经验,避免上述常见的设计误区,从而提高模具设计的质量,确保注塑生产的顺利进行。